Excitement About Alcast Company
Excitement About Alcast Company
Blog Article
The Ultimate Guide To Alcast Company
Table of Contents7 Easy Facts About Alcast Company ShownGetting The Alcast Company To WorkHow Alcast Company can Save You Time, Stress, and Money.Some Known Incorrect Statements About Alcast Company Examine This Report about Alcast Company6 Easy Facts About Alcast Company Explained
The subtle difference hinges on the chemical material. Chemical Comparison of Cast Light weight aluminum Alloys Silicon promotes castability by decreasing the alloy's melting temperature level and improving fluidity throughout spreading. It plays a crucial role in enabling detailed mold and mildews to be filled up precisely. Additionally, silicon contributes to the alloy's toughness and put on resistance, making it useful in applications where durability is critical, such as automobile components and engine components.It additionally improves the machinability of the alloy, making it much easier to process into finished items. In this way, iron contributes to the overall workability of light weight aluminum alloys.
Manganese contributes to the strength of light weight aluminum alloys and improves workability (Aluminum Castings). It is frequently utilized in wrought aluminum items like sheets, extrusions, and profiles. The presence of manganese help in the alloy's formability and resistance to cracking throughout fabrication processes. Magnesium is a lightweight component that provides strength and effect resistance to light weight aluminum alloys.
Getting The Alcast Company To Work
It enables the manufacturing of light-weight elements with excellent mechanical properties. Zinc improves the castability of light weight aluminum alloys and helps manage the solidification process throughout spreading. It improves the alloy's strength and hardness. It is frequently located in applications where complex shapes and fine details are essential, such as ornamental spreadings and certain vehicle parts.

The primary thermal conductivity, tensile stamina, yield toughness, and prolongation differ. Amongst the above alloys, A356 has the highest thermal conductivity, and A380 and ADC12 have the lowest.
The Of Alcast Company
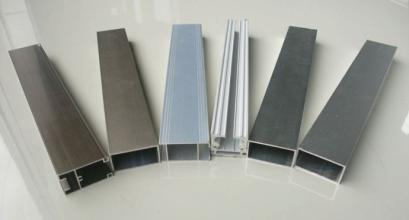
In precision spreading, 6063 is appropriate for applications where complex geometries and top quality surface area coatings are critical. Instances consist of telecommunication enclosures, where the alloy's remarkable formability permits streamlined and aesthetically pleasing designs while preserving architectural honesty. In the Illumination Solutions industry, precision-cast 6063 components create stylish and efficient lighting fixtures that require detailed shapes and good thermal performance.
The A360 displays premium prolongation, making it suitable for complicated and thin-walled parts. In precision casting applications, A360 is well-suited for markets such as Consumer Electronics, Telecommunication, and Power Devices.
Alcast Company Can Be Fun For Everyone
Its distinct homes make A360 a valuable option for accuracy casting in these sectors, enhancing product resilience and high quality. Light weight aluminum alloy 380, or A380, is a widely made use of spreading alloy with several unique features. It uses excellent castability, making it a suitable selection for accuracy spreading. A380 exhibits good fluidness when molten, guaranteeing complex and thorough molds are properly recreated.
In accuracy spreading, aluminum 413 radiates in the Consumer Electronics and Power Tools sectors. It's commonly made use of to craft detailed parts like smart device real estates, electronic camera bodies, and power device coverings. Its accuracy is exceptional, with tight resistances approximately 0.01 mm, making certain remarkable product assembly. This alloy's superior corrosion resistance makes it an outstanding option for outside applications, making sure lasting, resilient products in the mentioned sectors.
Little Known Facts About Alcast Company.
The light weight aluminum alloy you pick will significantly affect both the spreading procedure and the residential or commercial properties of the last product. Since of this, you must make your choice carefully and take an educated technique.
Establishing the most ideal light weight aluminum alloy for your application will certainly suggest weighing a vast selection of features. The initial group addresses alloy attributes that affect the production process.
Alcast Company for Beginners
The alloy you pick for die casting directly impacts several facets of the casting procedure, like how easy the alloy is to work with and if it is prone to casting defects. Hot breaking, likewise called solidification splitting, is a common die casting problem for light weight aluminum alloys that can lead to internal or surface-level splits or fractures.
Certain aluminum alloys are more prone to warm cracking than others, and your choice should consider this. It can damage both the actors and the die, so you must look for alloys with high anti-soldering buildings.
Deterioration resistance, which is already a remarkable characteristic of light weight aluminum, can vary considerably from alloy to alloy and is a necessary characteristic to think about depending on the ecological problems your product will be exposed to (Aluminum Castings). Wear resistance is another residential property typically looked for in light weight aluminum products and can separate some alloys
Report this page